|
|
Home > System > Autoclave > Composite Autoclave > CMAM series |
|
Autoclave |
Composite Autoclave - CMAM series
|
|
|
|
|
CMAM series is mostly used for manufacturing medium size composite materials. Vacuum line is connected to product in order to remove impurity before moulding. In the case of pressurizing for molding, CMAS series maintain constant pressure and temperature, to perform process in an optimum condition.
Ilshin Autoclave Co.,Ltd has ASME Pressure vessel manufacturing certification stamps(U1, U2, U3) , designs and manufacture equipment according to ASME regulations ensuring high safety and airtightness.
Ilshin Autoclave Co. Ltd designs the equipment with multiple options such as Magnedrive to maintain constant temperature, cooling coil for rapid cooling, automatic opening / closing cover, perfect insulation and heating for controlling temperature departure, automatic valve line for controlling pressure and multi-safety system.
Please refer to Options & Accessories for various options according to the purpose of use. |
|
|
|
|
Composite Autoclave Moulding Process |
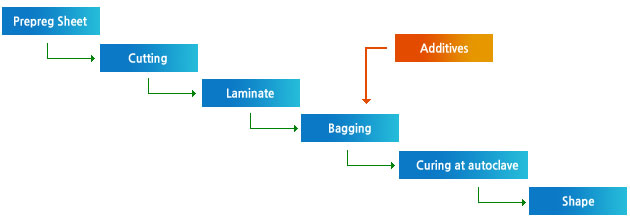 |
|
Composite Autoclave Moulding Lamination |
|
 |
|
Laminated molding & Bagging
• Prepregs + additive + sub-base material
• Reduce pressure to remove air bubbles when laminate 2~3 prepregs |
|
Features of Composite Autoclave |
Safety |
• Design and manufacture according to ASME, KGS and KOSHA
• Multi-line Pressure Control System for safety
• Continuous management by alarm list record |
Convenience |
• Minimize equipment size for efficient space use and application in various conditions.
• Controlling system controls all operations after putting material.
• Convenient cleaning by easy assembly / disassembly |
Controlling system |
• Control system using touch screen
• Accurate testing by automatic system |
|
|
Autoclave process variables |
Constant temperature |
• Minimize temperature departure by installing circulation fan. |
Pressure Accuracy |
•
Automatic valve line maintain pressure departure within 1.5%
|
Production |
•
Sample trays increase production |
|
|
Specification |
* CMAM 2000 Series |
Series |
Working Vessel
Internal Diameter |
Working Vessel
Distance
|
Temperature |
Pressure |
CMAM-2000-5000L |
2,000
㎜ |
5,000
㎜ |
200 ℃ |
9 ㎏/㎠ |
CMAM-2000-5000H |
2,000
㎜ |
5,000
㎜ |
200 ℃ |
20
㎏/㎠ |
CMAM-2000-7000L |
2,000
㎜ |
7,000
㎜ |
200 ℃ |
9 ㎏/㎠ |
CMAM-2000-7000H |
2,000
㎜ |
7,000
㎜ |
200 ℃ |
20
㎏/㎠ |
CMAM-2000-10000L |
2,000
㎜ |
10,000
㎜ |
200 ℃ |
9 ㎏/㎠ |
CMAM-2000-10000H |
2,000
㎜ |
10,000
㎜ |
200 ℃ |
20
㎏/㎠ |
|
|
* CMAM 2500 Series |
Series |
Working Vessel
Internal Diameter |
Working Vessel
Distance
|
Temperature |
Pressure |
CMAM-2500-5000L |
2,500
㎜ |
5,000
㎜ |
200 ℃ |
9 ㎏/㎠ |
CMAM-2500-5000H |
2,500
㎜ |
5,000
㎜ |
200 ℃ |
20
㎏/㎠ |
CMAM-2500-7000L |
2,500
㎜ |
7,000
㎜ |
200 ℃ |
9 ㎏/㎠ |
CMAM-2500-7000H |
2,500
㎜ |
7,000
㎜ |
200 ℃ |
20
㎏/㎠ |
CMAM-2500-10000L |
2,500
㎜ |
10,000
㎜ |
200 ℃ |
9 ㎏/㎠ |
CMAM-2500-10000H |
2,500
㎜ |
10,000
㎜ |
200 ℃ |
20
㎏/㎠ |
|
* Design and manufacture according to ASME, KGS and KOSHA
* Sample tray and cart are additional options.
|
※ Please contact our sales team to inquire about other specification |
|
Technical sales team : +82-42-931-6100 (Ext. 1) |
|
|
|
|
|
|