MUCELL とは超臨界状態の二酸化炭素や窒素を樹脂と混合したもので微細な発泡状態のプラスチックを成形する技術です。発泡セール(Cell)の微細化(5~50㎛)で広範囲の射出成形製品のコストが削減できる画期的技術として注目されています。科学発泡剤やフレオンなどを使用しない環境に優しい工程技術で、成形製品のSink Markなどの改善ができます |
|
|
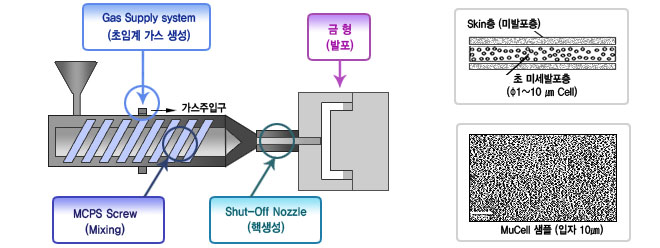 |
|
MuCellの概要 |
· MIT工科大学で開発された超微細発泡成形技術でアメリカTrexel INCと設備ライセンス締結(2001.1.10)
· 約20~30%のコスト削減と品質の改善などの利点があり、射出部分の機能性部品と自動車部品などで急速に拡散されている
· 約150個のEND USER、全世界の代表的射出機メーカー15個のライセンス確保
· 樹脂の射出、圧出、thermoformingに適用され、次世代Processing技術として脚光を浴びている |
|
MuCellの原理 |
プラスチック製品の重量を減らすために高分子材料の内部に微細な気泡(5-50㎛)を生成して製品を成形する技術(発泡技術) |
|
MuCellの特徴 |
コスト削減 |
• 樹脂の需要10〜20%削減、軽量化の効果4〜17%
• Cycle Time20〜50%削減(純粋冷却時間25%減少)
• 樹脂流動性の改善でClamping Tonnage50〜80%削減可能 |
品質改善 |
• 低圧射による残留応力除去での曲げとひずみなど防止
• 正確なサイズと製品デザインのFlexibilityの改善 |
材料物性補強 |
• 衝撃強度2倍、防塵・保温性能
• 優れた引張と圧縮強度 |
環境コスト削減 |
• CO₂, N₂を使用したSCF触媒でリサイクルが可能
• 超臨界低圧射出機として成形機の容量と消費電力を大幅に削減 |
|
|
MuCellの長所 |
• 成形材料に関係なく適用可能
• 高分子材料の粘度減少:最大60%
• 成形温度の低下:最大約70%
• 射出圧力の減少:30〜50%
• •保圧時間除去、Cooling Time最小化によるCycle Timeの減少
• 射出機Clamp Tonnage減少:40〜30%
• Sink Mark削除/曲げ防止
• 環境にやさしい技術 |
|
MuCellの成形技術 Process |
段 階 |
内 容 |
1段階:ガス注入 |
- 超臨界状態のN2又はCO2 Gasをシリンダーに注入
- ガスが高分子に迅速に溶解される |
2段階:セール生成 |
- 発泡ボールが生成される段階
- 本来の発泡成形に比べ、非常に多く形成される
- この時、均一な発泡ボールの形成のため、高速Pressure Dropが必要 |
3段階:セール成長 |
- 発泡されたセールが形成される段階
- 発泡Cellは、プロセス条件によって制御される
- 正確な温度と圧力の制御が要求される |
金型に注入して成形する段階
- 別の金型の修正は必要ない
|
- 金型に注入して成形する段階
- 別の金型の修正は必要ない |
|
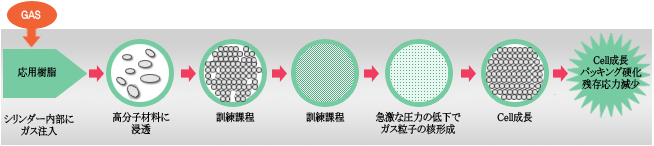 |
|
発泡方式 |
成形法 |
状態 |
成形方法の原理 |
欠点 |
利点 |
ガスインジェクション |
部分的
中空 |
成形後、冷却固化する前に、
金型内の溶融樹脂中にガスを注入、部分的中空を形成 |
- ガス注入装置が必要
- 特許承認契約が必要
- 部分的中空で少ない軽量化
- 高圧ガス法適用 |
- 陥没防止
- 軽量化(約5〜10%)
- 強度向上 |
化学発泡剤に
よる発泡 |
発泡
80~150㎛ |
一般の成形法とほぼ同じ方式。
発泡剤をドライブレンドするが発泡剤混合樹脂で通常の射出成形を行う
|
- 環境に影響を及ぼすガス発生
- 外見が悪い
- 成形サイクルが長 |
- 普通の成形技術だけで可能
- 軽量化(約5~50%)
- 断熱・遮音効果 |
Mucellによる
発泡 |
発泡
20~50㎛
|
超臨界流体を射出成形器のシリンダーに注入させ、発泡剤が得られる |
- ガス注入装置が必要
- 特許承認契約が必要
- 特殊射出成形器が必要
- 外見が悪い
- 高圧ガス法適用 |
- - 軽量化
- エネルギー節約
- 陥没防止
- 成形サイクル短縮
- 低温形成
- 化学発泡剤・フレオンが要らない |
|
微細
10㎛ 以下 |
|
|
- 構造や強度部材に対する適用 |
|
|